Lechler’s Website:
START:
|
 |
|
|
|
|
|
 |
 |
 |
 |
 |
 |
 |
 |
 |
 |
 |
 |
 |
|
 |
|
|
Engineering - Electronics - Content :
|
|
|
|
Electronic Power Supply ,Switchers, Converters and low frequency Circuits, Content:
|
|
|
|
Open loop for Switching regulators for power supplys : German Patent DE3609731
The closed loop stability of switching regulators is not easy
to get. Especially if the stability requirement of the output voltage is below 1%. One can overcome this problem by using an open loop, witch controls then the most of the output voltage deviations. This then allows
to reduce the feedback gain at a value below ringing of the loop. Figure 1 shows the circuit of a typical switcher with a closed- loop-amplifier F including stability networks, current feedback and circuits.
The pulswith is produced by means of a saw tooth voltage having an amplitude of Vz. The amplitude of this saw tooth voltage now is controlled from the input voltage via a correction amplifier A. The result is a
constant output voltage, even without a closed loop. The closed loop gain can be reduced and stability problems are minimized.
Figure 1 Switching regulator with open loop
Fig. 2 Equations of switcher open loop
Return:
|
|
|
|
Ripple-regulator reduces bus ripple without electrolytes.
Electrolytes
are the big reliability problem in power conditioners. If the frequency of the produced ripple is high enough to be filtered with plastic-capacitors, the problem is solved. But in some cases, this capacitors are
to big and/or not useful at higher temperatures. A ripple regulator may be solve this problem. The ripple regulator is a voltage regulator working only from the AC on the output bus. The feedback must
therefore be fast enough to regulate the ripple to minimum. A switching or big analogue-transistor is not necessary to run a ripple regulator. A little transformer driven by a small transistor, will do the
job. If the inrush current of the to the output is controlled, a very small transistor can be used too. C1 and C2 are SMD-high frequency de-spiking capacitors. The loop of the feedback must be fast enough
to regulate the ripple frequency. A feedback network has to be used to ensure stability. Fig. 1 shows a tested circuit for a 3A/12V-switcher having an output-ripple of 20 kHz. The ripple was reduced by a factor
of 500 using a E16 high my-core.The same circuit can reduce 50 Hz ripple from simple power-supply’s without big ripple-capacitors .The ripple transformer then becomes relatively large, but can
encounter very high temperatures.
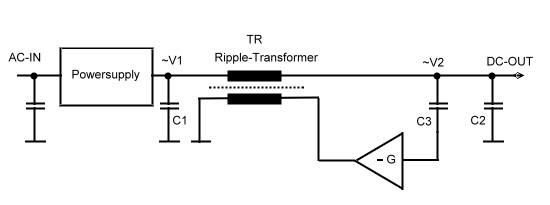
Fig. 1 Ripple-regulator
Return:
|
|
|
|
Fast switcher power cells FSC for communication power supply’s, (FSC= fast switcher circuit)
A new generation of power supply switchers is presented. This switchers are based on the electronic
programming of several pulses to switch power switches on and off. The function of the programming is mathematically correlated to requirements of a power-cell. The basic function is explained in Fig.1 showing
the difference between regular power switches as buck, buck boost , boost or enable .The regular switcher has on and off time where the mathematical relation between both is simple only the difference between
both ,whereas the sum of both times is the switcher period. The FSA switcher has tree switches and tree switching times. The sum of the three times is the switcher period . The three times are somehow programmed
mathematically by an equation or by means of an electronic device.
Fig.1 Usual switcher timing Fig.2 New switcher timing ####
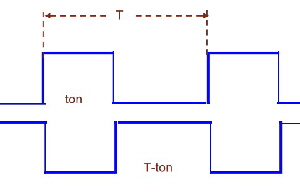 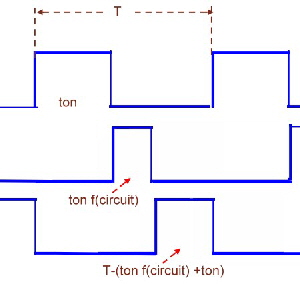
To get such a switcher run, we must first find a circuit which combines
the classical buck and the boost mode.The result is shown in Fig.2 The Function is as follows: We find 2 electronic switches, S1 and S2. S1 closed, led the charging current I1 flow through L/x. S1 open and S2
closed is the boost discharging mode .The coil de charging current from L/y is I2 . The energy in the inductor is added to
the battery voltage and we get Va > Uo. If both switches are open , the de-charging is continued from L via D1 and I3.
This is equivalent to the Buck mode and we get Ua<Uo. In a balanced condition where the regulator feedback is closed, the coil will never be discharged completely . Now we lo ok to the Current trough the inductance during the whole cycle.
Fig.3
Fig.2 The FSC buck boost regulator
A simple mathematical relation is a factor k. Then we get the following simple time relations:
- S1 on during the time :

- S2 on during the time :

- S1 and S2 off :

Fig.3 Balanced coil current
We get the static equation setting the changing currents to zero:
Fig.4 static equations
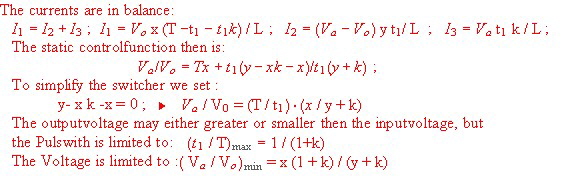
If we want watch the dynamic behaviour, we decrease the control pulse t1 very hard with a negative time jump
.The result is a time jump on each of the three switcher times .Fig.6 shows the result at Io. As the time period T is constant,
we get a current increase delta I. Fig.7 This increase in current versus time , shows the actual switcher speed. Now we
compare this current increase to an virtual single analogue coil Fig.8 and can compute the analogue voltage regulator transmission F(s) of the power cell ,Fig.9 , to optimize the regulator loop.
Fig.5 Frequency response of the power cell
Fig.6 Computing of the virtual analogue inductance of the power cell
This result shows , that the new power cell is very fast reacting to distortions, that means, that the closed loop will
counteract very fast too load jumps as it my happen in a communication system using switched power amplifier channels
.Under this conditions, a slow switcher regulator my produce dangerous voltage overshoots. By means of the inductance
Lo , we can certain the analogue regulator control circuit of Fig.9 which is a normal low pass as usual . Vin here is the input feedback voltage to compute F(s), not the DC input.
Fig.7 Equivalent analogue frequency behaviour circuit
Fig.8 Computing corner frequency and roll off

This power cell is only one example of dozens of possible new switcher cells which are possible especially if the factor k is
made nonlinear by means of an OPAMP:
Fast buck boost switcher regulator cell #1
If the primary coil of a conventional buck boost switcher is tapped, we get the circuit of Fig: 9.
If we make:
- S1on >>> t1; S2on >>> (T/n)-t1
- y=(sqr)N/(sqr)Ny and x=(sqr)N/(sqr)Nx
- n >1 ; T/n = end of charching time.
we get:
- Ua_/ Ue_ = (x+(t1/T)*n[1-x])/ y[n-1])
- Lanalog = ((sqr)n/y*sqr[n-1]) (Lanalog = virtually Low-pass inductance l
- Lanalog is constant and depents not on voltages.
- In the common buck boost circuit, Lanalog depents on the voltages Lanalogcom = sqr(Ua/Ue +1);
- Lanalog << = Lanalogcom .
This means, the new circuit is faster than the common circuit!
Fast switcher buck regulator Cell #9
If the coil of a conventioal buck switcher is tapped, we get the circuit of Fig:10
If we make:
- S2on >>> t1; S1on >>> T-t1-t1*k
we get:
- Ua_/ Ue_ = 1+(t1/T)*[(1/x)-1-k)]
- if we chose: y = ((x*k)+x-1)/k
- Ua/Ue = 1-t1/T
- Lanalog= L*x
The fast buck switcher regulator Cell #13
If the coil of a conventional buck switcher is tapped and transformed, we get the circuit of Fig:10
If we make:
- S2on >>> T-t1-t1*k; S1on >>> t1
we get:
- Ua_ / Ue_ = x*T /( t1*(y+k);
- Lanalog =sqr(Ua/Ue)*1/sqr(x);
If we make:
- S1on >>> T-t1-t1*k; S2on >>> t1
we get:
- Ua_ / Ue_ = 1 /( 1-(t1/T))
- Lanalog / L =sqr (Ua /Ue)
The fast buck boost switcher regulator Cell #14
Tapping the common buck boost switcher cell leads to Fig 11:
If we make:
- S1on >>> T-t1-t1*k; S2on >>> t1
- x = 1/ (k +1)
we get:
- Ua_ / Ue_ = x*T / (k*y*t1)
- (Lanalog /L ) = (Ua/Ue)* 1/ (1-((x/y)*(Ue/Ua))
- if we make k=m*Ue we get Ua= (x/m*y) *(T/t1);
- Then we get: Ua = const. The input voltage variation is eliminated by means of forward regulation.
The fast boost switcher regulator Cell #15
Tapping the common boost switcher cell leads to Fig 12
If we make:
- S3on >>> T-t1-t1*k; S1on >>> t1; S2on >>> t1*k;
- y = k*x / (k +1)
we get:
- Ua_ / Ue_ = 1/( 1-(t1/T*(1+k));
- (Lanalog /L ) = 1/y
The fast boost switcher regulator Cell with energy-back-flow #16
The common buck switcher cell with tapped secondary winding leads to Fig 13
If we make:
- S1on >>> T-t1-t1*k; S2on >>> t1;
- x =1+k*(y+1)
we get:
- Ua_ / Ue_ = 1/ T*(1+k)
- (Lanalog /L ) = sqr(Ue/Ua)
- for instance, If Ua / Ue = 0.25, Lanalog = L*0,065; for the common boost swicher cell we will get
- Lanalogcommon = L*1,56;
A fast switcher regulator Cell with energy-back-flow #17
A new switcher cell with energie feedback leads to Fig 13
If we make:
- S1on >>> T-t1-t1*k; S1on >>> t1;
- 0 = y-x-kx
we get:
- Ua_ / Ue_ = (2*t1/ T) -1 ) /(t1/ T);
- (Lanalog /L ) = (Ue/Ua)
The efficiency optimized fast switcher regulator Cell #24
A new switcher cell working only in the upper output-voltage range, leads to Fig 14
If we make:
- S1on >>> T/n =const.; S3on >>> t1; S2on >>>T-T/n -t1;
- 0 = y-x-kx
we get:
- Ua_ / Ue_ = (1/n) / (t1/T*(1-y) + x/n +y*(1-1/n)
T
he fast switcher regulator Cell having controlled loading and controlled deloading #36
Working with 4 switsches to control charching and discharching time, Fig.15
If we make:
- S11on >>> T*(1-1/n)-t1*k ; S9on >>> t1; S8on =T/n -t1; S10=t1*k;
- 0 = ky-zk-x+1
- n >>> choose for ETA opt >>> ETA =const;
we get:
- Ua_ / Ue_ = (t1/T [1-x] +x/n ) / (z-(z/n)+x/n)
- at n=1,25; x=0,2; z=2 >>> k(2-y)= 0,8
- Ua_/Ue_ =(0.8*t1/T + 0,16) /0.56
T
he fast switcher push pull regulator Cell #32
Working with 4 switches in a push pull boost converter give high current on the output Fig.16
If we make:
- S2on >>> T/2 -t1; S1on >>> t1; S4on = t1; S5on =T/2 -t1;
- Ua_/ Ue_ =(2*t1/T*(1-x)+(x+y)) /y
In the similar manner, the shown circuits may be modified to a push pull converter.
Return:
|
|
|
|
Combine buck and boost power cells, to optimize efficiency. German Patent DE 2941 009 C2
Wide regulation switchers, have the
problem of low efficiency at the end of the input voltage range.This decrease can be up to 10 % of the maximum efficiency. The combination of different power cells
can overcome this problem. If for instance a boost cell runs at the lower values of the input voltage range, and the buck mode runs at the lower input voltage, one
can get an efficiency as Fig.1 shows. But combining two different cell types may be a problem. I propose to combine the cells by means of the
electronic control circuitry. If we divide the saw tooth voltage of the puls modulating circuit in two parts , switching the clock frequency between buck and boost
mode, the power mode will automatically change at the midst of the input voltage range.The circuit is shown at Fig.2. We see the 2 buck switches directly connected
to the voltage input. The boost switches are connected to the output transformer. The coil L is used in both modes. D is the free-wheel diode necessary in the buck
mode.The two boost transistors act as push pull switches for the transformer. In the boost mode, the switches are both in the on condition, what
cancels the transformer off. The buck switches are saturated and the coil L is charged with the input voltage.The clock is divided using a toggle flip flop
to drive the different cells via NOR logic devices.
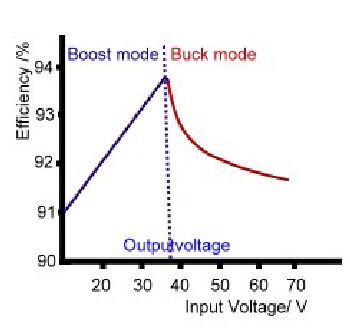 |
Fig.1 Efficiency of Buck and Boost combined cells.
Fig.2 Logical circuit, combining buck and boost cells.
Return:
|
|
|
|
Regulated High Voltage DC Converter has low output ripple . German Patent DE 4302598 C2
Normally, a regulated DC
Converter is controlled changing the duty cycle between inductor charging and discharging mode. During the charging mode of the coil, the
energy on the output is derived from an energy storage capacitor.This usual way of regulating, leads to a certain amount of ripple on the output
voltage. In low output voltage converters, this ripple can be easily reduced . But if the output voltage is in the kV-range, the ripple filters are
voluminous and unreliable. A bridge converter power cell, can be modified to work as pumping converter controlled from a duty cycle change, whereas the
output duty cycle is constant. Excessive energy in a charging inductor is pumped back to the input voltage source. In using this circuit, the ripples on
the output are reduced to very small spikes even during primary duty cycle variations. An other advantage is the increase of the feedback control speed,
because no ripple must be filtered out in the loop circuitry.
Lets look first to the circuit of the bridge converter at Fig1. We have the output transformer
Fig.1 Pumping bridge converter
We have the output transformer Tr1, the switches S1, S2, S3, S4, and the energy back transformer Tr2 and two pumping
coils L1 and L2. The switches S3 and S4 are periodically switched with a duty cycle of 1:1, whereas the switches S1 and
S2 get time variation control pulses. Fig.2. They switch the load via the transformer Tr.1 during charging and de-charging
of the coils, that means energy is transferred to the output at the time where energy is pumped from and back of the
source Vin. .
Fig.2 Bridge converter drive diagram
Return:
Combine push pull and bridge converter as pulswith regulator.
As the regulated pumping bridge converter of the above circuit needs a lot of components , I try to simplify this bridge
converter into a combination of bridge and push pull converter. The output transformer will have two more windings having
less turns then the main primary winding. If we change the power switches between the different primary windings, we get
a buck boost converter with tree different charging times of a energy storage coil L. The result is the same as above,
constant duty cycle for the output voltage. Fig.1 shows the circuit. The switch timing is somewhat different from Fig.2. If I
will find the time, the timing of the switches will be calculated and the time to voltage control formula from the balanced
currents in the coil L shown.
Fig.3 Regulated Push pull bridge converter
Return:
|
|
|
|
Regulated DC-Bridge Converters in Buck Mode. German Patent DE 3808432 C1
Classical Bridge DC to DC Converters are not regulated. But due of their four switches,
they are excellent configurations to be pulswith regulated in many configurations. Sure an energy inductance is necessary, where the energy
is stored stored , transformed and somehow brought back into the current cycles. Either back to the battery or to the output. If it pumped to the
output there are two possibilities, either the coil energy is added as parallel current (buck-mode) or added as series voltage (boost-mode).
Here are three pulswith controlled Bridge Converter Circuits which work in the buck mode. Fig.1 shows a controlled bridge converter with center
tapped output transformer, where the buck current flows from the energie storage coil L via D2. D2 only is a de-spiking diode. The output voltage
equation is the same as in a conventional buck free-wheel converter: Uout / Uin = (ton / T) r ; Fig.2 shows the switching diagram. It is obvious,
that the transformer is periodically switched to the input voltage via S1 / S2 and S3/S4. During this time, L is loaded. The discharging of the
Coil then comes in the push pull mode versus S1 and S3.
Fig.1 Buck regulated bridge converter 1
Fig.2 Switch drive of the regulated bridge converter 1
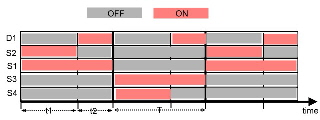
An other circuit is shown at Fig.3. Here are the push pull
windings on the storage coil, not on the transformer.This simplifies the transformer . In doing so, the digital drive must be different. Fig.4
In an other circuit, the complexity of transformer and coil is
reduced, using the primary winding of the transformer T for energy injection by means of better circuitry. Fig5 In this
circuit, the same digital drive as in Fig.2 is valid. S1 and S4
are used, to switch the discharge energie of the coil into the the output transformer.
Fig.4 Digital drive of Fig.2 and 5
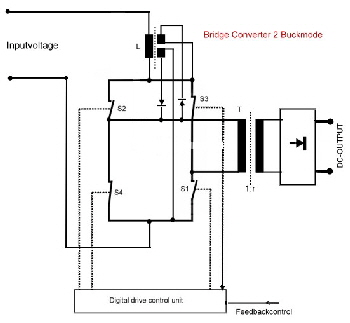 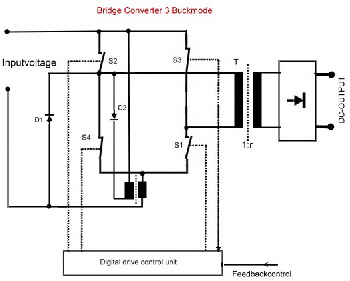
Fig.3 Buck regulated Bridge converter 2 Fig.5 Simplified buck regulated bridge converter 3.
Return:
|
|
|
 |
 |
 |
 |
 |
 |
 |
 |
 |
 |
 |
 |
 |
 |
 |
 |
 |
 |
 |
 |
 |
 |
 |
 |
 |
 |
|
 |
|
|
Electronischer Brückenwandler arbeitet als Aufsteller
German Patent DE 3808433
Zur Versorgung von Mikrowellenröhren mit Hochsannung wird üblicherweise ein DC- Wandler verwendet.Iin
dessen Transformator wird die Versorgungspannung der Röhre auf die notwendige Höhe transformiert. Für
kleine Geräte mit Miniaturtranformatoren wird dies bei Spannungen über 3kV wegen der notwendigen Isolation
schwierig. Wenn der Wandler zusätzlich im Boostmode arbeitet ,kann der Ausgangstransformator wesentlich
kleiner werden; da die Primärspannung grösser ist. In Fig. 1 ist ein Brücken-Wandler der als Boostegler arbeitet,
.und dessen Ansteuerung gezeigt, Fig.2 zeigt den notwendigen Steuertakt. Während der Brückenwandler mit S3
-S5 normal im Gegentakt arbeitet, arbeitet S1 in jedem Brückentakt als pulsbreiten geregelter Boostschalter.
Electronic Bridge Converter works as Boost Regulator, 
To supply microwave tubes with their working voltages, a high-voltage DC converter is used. It is common to
transform the supply voltage of the tube in the converter’s transformator to the necessary height. For small
devices with miniature transformers, this is difficult at voltages above 3 kV because of the necessary insulation
.When the converter is operating in boost mode, the output transformer can be much smaller. In Fig. 1, a
converter bridge converter and its control is shown, which works as a boost regulator. Fig.2 shows the necessary
control clock sequence. While bridge converter with S3-S5 is normal working in push-pull mode, works S1 in
each bridge Phase as pulse width controlled boost switch.
Fig.1,2 Bridge Converter-Boost-regulator / Brückenwandler als Hochsteller
Return
|
|
|
|
Transmission of Sample and Hold
As it is well known, a sample and hold takes signal probes and keeps the amplitude
of this probe constant until the next sample peak. Fig.1 To use this circuit in a feedback of a power supply, one has to know the amount of negative phase the sample and hold will produce in a loop. As the S+H is periodically switched, periodically Phase jumps of 180 degree appear at the multiple of the sample frequency. Fig.2 Whereas the Gain has a slope of -20 dB / Dec.

Fig.1 Sample and Hold Probes
Fig.2 S+H Gain and Phase
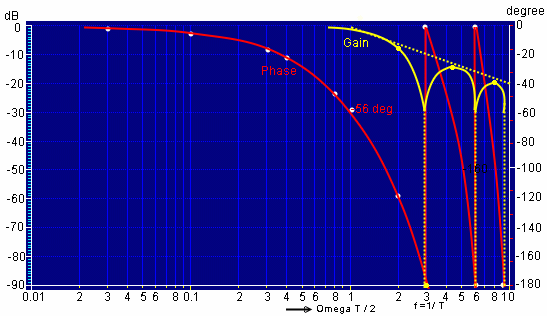
Return:
|
|
|
|
Sample and Hold improves Switcher Loop.
Feedback loops in general , in power supplies or
some other analogue regulation loops, must be cleaned from ripples, fast distortions and short time disturbances. This is not really part of
the necessary system loop, but an important part for the electronic loop circuits . Normally little low passes or integrator circuits are
used to cut the ripples off. But this circuits will produce negative phases up to 90 degree in a loop and deteriorate loop quality. To avoid
this negative phase, a sample and hold can be used instead. Sure the sample and hold produces negative phase too, but the total loop
phase will shown an improved loop condition. Regulation using Sample and Hold in the Feedback and digital software is called DDC
(Direct Digital Control), but in this application, the sample and hold is used in the analogue feedback part of a switcher power supply loop.
If the sampling frequency is chosen to be 10 times the power supply ripple frequency, the negative phase in the loop due of S+H may be only -10
degree. The saving of Phase due of the S+H, can improve the stability of the regulator and its reaction speed..
Example: A switching regulator output has 500 mV
ripple. After dividing it with a resistor loop divider, the ripple is 250mV. The circuit sensitivity of the regulator is limited
due of gain and latching effects, to 20 mV. Necessary damping of the ripple d = 20dB. A 20 dB first Order low pass is useful to damp this
ripple. The green lines of Fig.1 shows the gain and the phase of this low pass. The additional negative phase for the loop is 10 to 40
degree.(green) Using a sample and hold instead of a low pass, the ripple becomes almost zero and
the negative phase will be only 0 to 10 degree due of sample and hold (Red). This makes it possible, to make the regulator 5 times faster if using a sample and hold in the loop.
Fig. 1 First order low pass compared with a sample and hold
Example of a buck-regulator with sample + hold in the loop.
Fig.2 shows the block diagram of a switching regulator having a simple and hold in the loop.
The numbers of blocks are.
- 1 Power cell
- 2 sawtooth-generator
- 3 Pulswith modulator
- 4 Phase correction
- 5 S+H clock
- 6 S+H
- 7 Loop Gain
- 8 Loop low-pass
Without 5 and 6 the circuitry is the same as a normal switcher circuit. The sample and Hold is synchronized
from the Power switches frequencys sawtooth. Fig.3 shows Gain and Phases of the single devices and the total
loop. The S+H frequency is 10 times the clock frequency to prevent spikes. At least, is the loop very faster as a
normal switcher loop and has a better stability.
Fig.2 Switching-regulator with Sample and Hold
Fig.3 Open loop Bode plot of Fig.2
Example of a buck-boost regulator, with sampler in the loop; German Patent DE 3328840 C2
We have seen above, that the low pass in the loop which eliminates the ripple from the output-voltage makes the
stability problem in switcher regulators due of producing up to 90 degree of negative phase. Above we used a
standard sample and hold circuit to overcome this problem. An other way is, to sample the output voltage and
build a pulswith-modulator controlled from this output voltage. Fig.4 shows the circuit of a buck boost regulator.
In this circuit the comparison sawtooth voltage is sampled and renewed by means of an integrator and two
comparators establishing the Power transistor to control the Power transistor.
Fig.4 Buck-Boost regulator with sampled sawtooth
Example of switching regulators, with high grade inputfilter; German Patent DE 2950340 C2
The ripple filter loop problem can be solved the conservative way, increasing the filters grade to match the phase
to the switchers data. If the filter has the form of,
the switcher loop can be optmized with a lot of filter- parameters. An example is Fig.5 : Filter Data.
There are many ways to realise the filter, on way is shown in Fig.6 : Loop filter circuit
As an Example, the open loop of a buck switcher having the filter of fig 6 in the loop is Fig.7 : Total switcher loop
Return:
|
|
|
|
RTL-Logic improves reliability in Power Supply’s
Power supply's sometimes need logic circuits. Of course at low voltage
supply’s, we use the customary IC’s. But for high Voltage supply’s sometimes is it more reliable to use
simple RTL logic and make their circuit a direct part of the Power supply circuit. Here are a few classic RTL circuits to improve
the reliability of Power supply’s for traffic or space applications.
Fig.1 Classical RTL logic circuits
#1
|
|
NAND
|
A
|
B
|
out
|
1
|
1
|
0
|
1
|
0
|
1
|
0
|
1
|
1
|
0
|
0
|
1
|
|
#2
|
|
NOR
|
A
|
B
|
out
|
1
|
1
|
0
|
1
|
0
|
0
|
0
|
1
|
0
|
0
|
0
|
1
|
|
#3
|
|
NOR
|
A
|
B
|
out
|
1
|
1
|
0
|
1
|
0
|
0
|
0
|
1
|
0
|
0
|
0
|
1
|
|
#4
|
|
NAND
|
A
|
B
|
out
|
1
|
1
|
0
|
1
|
0
|
1
|
0
|
1
|
1
|
0
|
0
|
1
|
|
FIG.2 Truth table of RTL logic
Return:
Simple DC-Circuit improves TWT live-time.
German Patent 1566020
The TWT (Traveling Wave Tube) is the last tube of the electronic tubes family are still in use. It is required to
build high power GHz transmitters with low distortion. But their draw back is the decrease in power output over
the life due to a reduced electron beam. Using a resistor and a feedback circuit we can compensate the decrease
of RF- Power. Fig. 1 shows a diagram of a simplified TWT and its P ower Conditioning. The grid 1 voltage sets
the operating point of the TWT and its output power. If the cathode emission decreases
during live-time, the collector current IC(1-n) will become smaller. Now, this current is measured by a resistor and fed back as a
voltage to the power supply grid 1.
The Grid 1 Voltage then becomes a function of
tube lifetime, ad electron emission is regulated.
VG1sum=Vg1+V(f(Jc(live of tube)))
Fig.1 TWTA Circuit using Grid feedback.
Return:
TWTA preheating time is made proportional to power interrupting time.
Simple Circuit can measure main power interrupting failure without an auxiliary battery.
German Patent DE 3332940 C1
High-power transmitters TWTA's still have a tube that must be preheated after switching on. This preheating time
normally is about 3 to 10 minutes. This is a problem in case of short main power interrupting failure in the seconds
range. In this case ,a preheating time of 5 minutes is unnecessary, but the preheating time should be :
Tfilament =tfailure* Tpower. To realize this ,the main power interrupting time must be measured. Normally one
would use a digital timer supplied by a battery, to measure this time. But then, due of the battery, the reliability of
the TWTA becomes low. The question is, can we measure the main power interrupting time without the use of a
battery? The solution is: The trick is the use of a dual slope integrator using a plastic capacitor C1 in the feedback. See the circuit of Countersign regular condition, C1 is charged and the relay Rel =on. In case of main power
failure, Rel = off, C1 discharges over R4, R5, see Vc. After that when the main- power is on again, C1 is charged
again. Using Comparator K1, the level of discharged C1 voltage becomes a measure of the power interrupting time. See Fig.2
If the time constants of C1 and the comparator K1 level is used properly, the output of K1 can directly switch on
the preheating process of the TWTA.
Return:
|
|
|
|
How to build a fail save DC- Switch
Single transistor DC-power electronic switches my fail, and stop the car, the
train or their control circuitry during traffic control. This may lead to terrible events. To prevent such live important failures, the single transistor switch
may be replaced by an quad switch, designed for space applications. Quad means, we use two
power transistors in series and the same arrangement as an paralleled path. So we have
four useful transistors. See Fig.1. This design is redundant for short and open failure. To drive
the bases of the power switches, we use transistor series circuits too. Now wee see, at
least two transistors must fail to get malfunction .The control voltage must be able, to supply 7
transistors bases even in case of base breakdown. As I have designed this switch in
the seventies npn transistors have been used, but as this is only an example of redundant circuitry,
modern MOS devices may be used instead, but high reliability only comes from discrete components.
Return:
Fig.1 Quad DC.switch
|
|
|
|
A Phase regulated high power DC-Converter needs smaller power-transistors
Phase regulation in a DC Converter is a
practical and helpful method to distribute the input DC Power in into paralleled DC-Converters, consisting of small and cheap
switching transistors. Such regulated DC converters have a very high efficiency because, the used unregulated push pull
converters can have an optimal eta of > 95% . Fig.1 shoes a block diagram of a phase regulated 2kW-DC-Converter, using two
standard push pull converters, where the drive voltages of the power switches are shifted in phase as function of the
feedback-control-voltage. The Square wave voltages of the converters are added by means of a power transformer. Fig.2
shows the output AC voltage (blue). The DC-Voltage, must be stored in a buck switcher L-C-Diode circuit. This circuit will
decrease the efficiency a few percent. Total efficiency is about 93%: The buck storage formula is valid there, but due of the
voltage adding, the ripple frequency is twice the converter frequency, which eases ripple filtering. The phase control is
easy to realize, using standard logic circuitry. One converter is driven directly from the square wave clock. This Clock
produces a saw tooth too. The control DC- Voltage and the saw tooth create a pulswith controlled voltage , which triggers a
toggle flip flop which creates a new phase depended 1:1 square wave
Fig.1 Phase regulated DC- Converter
Fig.2 AC-Output voltage
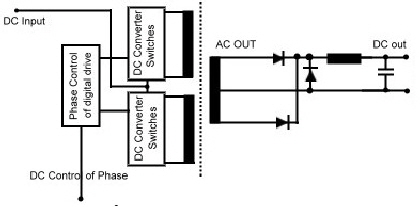
Return:
|
|
|
|
A high Power Latching Relays Driver for Wave-guide Switches. German Patent DE3040806 C2
Latching Relays come out in
different sizes, they have two switching magnets, which changes status by means of two coils. Two change the status a
short time drive current must be flow through one of the status coils. In case of a system voltage loss, latching
relays keep its position, without any power. There fore, they are a good solution to replace storage elements in electronic
equipments to prevent standby power. Small latching relays can be driven directly from an triggered mono stable Integrated
Circuit. In case of a bigger Relay, driver transistors are necessary. To prevent a separate power supply in 12/24/48 Volt
circuits, to feed the Integrated circuits, the latching relays driver transistor can be used to produce a switching impulse.
Fig 1 shows a driver circuit used to switch a 24 Volt Wave-guide latching switch. This driver is very robust and may be used in
traffic electronics too. It had been used manifold in high power TWTA’s.
Fig.1 Wave-guide Latching relays driver
To change the Relays status from A to B, the switch S is set to B. The de-charging path R2 of C1 then is opened and C1 is
recharged via the Base of T2. Due of this, the relay goes to B and the shorted T2 de-charges C2 and opens T4, blocking
T3 and A. In case S is on A, the function is vice versa. To prevent malfunction at higher temperatures, the leakage current of
C1/C2 must be kept low.
Return:
|
|
|
|
How to regulate the classical push pull converter
The circuit of the classical push pull converter using two switches
and a transformer is almost 60 Years old and still used today. Fig1. remembers the function: Two Power switches S1 and S2 have
the push pull modes on and off and drive a transformer with a rectangle power . A simple coil improves it to a normal boost
regulator if we overlap the two switches for a variable short time. during this time, where both switches are on the
transformer is canceled, and an inductance is loaded on the input voltage. Its energy is added to the output during the
push pull mode.
Fig.1 Classical push pull converter. Fig.2 regulated push pull converter
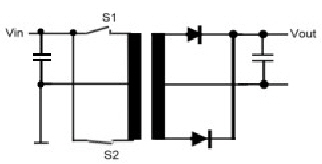 Cload
ratio, Lcu, Rcu
To compute the values of the boost components, the outputcapacitor must be the series connection of transformer datas (Rcu + Lcu + Cload ) transformed with ratio(SQR)
Return:
|
|
|
|
The Frequency behaviour of the Power Supply Boost Switcher Power Cell
Due
of its simplicity and its very high efficiency of almost 100 % , the original boost switcher is very popular. But the closed
loop behaviour is not as easy . To realize it in a high gain loop, some circuitry is necessary to get stability. First is to
know the analogue transmission behavior of the boost power cell of Fig.1. The control transmission is the path of the pulswith
ton / T to the output voltage Vout. As the feedback control loop is analogue, we must find a analogue model
for the power cell feedback transmission. As the equations at Fig.2 shows the control transmission is depending on the
working point of the power cell, that means the input voltage value. The given transmission formula can be directly used in an
analogue bode consideration as F(s) using Fig.3. What we find here is at least a roll off of -20 dB and a damping factor which
is important for stability depending on all components. That means to get the switcher stable, the values of all
components must be proper selected. Further it is obvious, that the losses of the charging capacitor produce a positive loop
phase. Therefore the capacitor loss stray values, must be carefully watched.
Fig.1 Booster power cell
Fig.3 Analogue Feedback Block
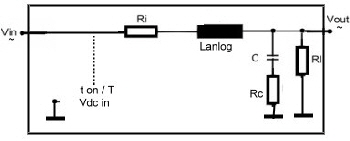
Fig.2 Equations of the booster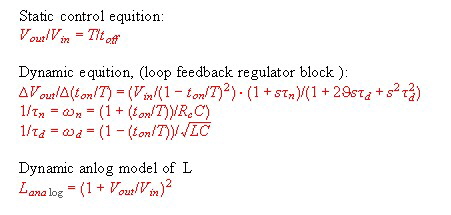
Return:
|
|
|
|
The Frequency behaviour of the Power Supply Buck Switcher Power Cell
The
most used power supply switcher cell is the buck switcher. This circuit is simple and robust, and so is the frequency behavior
if used in a feedback loop. Link to feedback formulas
The well known buck switcher cell circuit is shown at Fig.1. The power switch is
continuously switched on during the on time ton. The Question now is, what will happen, if ton varies a small amount at
different frequencies. A balance current consideration leads to the result of Fig.2. which indicates, the regulator block of
the buck cell is a low pass equal to the switcher circuit of Fig.1. having a steady state pulswith ton / T and Lanalog = L, see
Fig.3
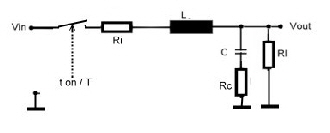 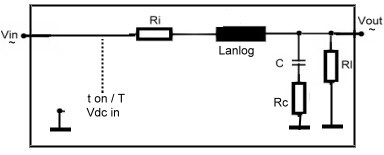
Fig.1 Classical Buck Power cell
Fig.3 Analogue Regulator block of Buck cell
Fig.2 Loop frequency behavior of the Buck cell
Return:
|
|
|
|
DC-Wandler Einschaltstromstoß ist angepasst an die Transistor second breakdown spec..
Patent DE 31 31429 C2
Die Hochspannung zur Versorgung von Mikrowellenröhren z.B. Wanderfeldröhren wird aus Platz und Gewichtsgründen
in Transistor DC-Wandlern erzeugt. Die Schalttransistoren der Wandler sind meist bidirektionale Transistoren. Solch ein
Wandler ist in Fig.1 gezeigt. Die Leistungstransistoren sind #10,11. Beim Einschalten der Versorgungsgleichspannung
,durch den Schalter #13, muss der Wandler zwei gegensätzliche Bedingungen *1 und *2 erfüllen.
- *1 Der Einschaltstrom-stoß des Wandlers darf die Leistungstransistoren nicht schädigen.
- *1 Der Einschaltstrom-stoß des Wandlers während der Einschaltzeit, darf die Second- Breakdown Grenze der
Leistungs-Transistoren nicht überschreiten.
- *1 Der Einschaltstromstosß in bestimmter Zeit, muss so niedrig sein wie möglich.
- *2 Nach dem Einschalten, müssen die Ausgangsspannungen des Wandlers in bestimmter kurzer Zeit ihre Sollwerte
erreicht haben.
- *2 Der Einschaltstrom-stoß in bestimmter Zeit, muss so hoch sein wie möglich.
Diese zwei Bedingungen, können nur mit einem Kompromiss gelöst werden. Fig.1 zeigt einen Wandler, in dem ein
Kompromiss zwischen *1 und *2 realisiert ist.
Die Komponenten #10,11,12,20,21,15,16,17, stellen den eigentlichen Wandler dar. Um die Bedingung *1 zu erfüllen,
wird der Einschaltgsstrom-stoß hart begrenzt, und zwar mit der Schleife der Komponenten #31,32,33. #32,33 sind die
Verstärker der Konstantstrom-schleife. Um die Bedingung *2 zu erfüllen wird der Einschaltstromstoß zeitabhängig
geschaltet. #45,41,48. Der Einschaltspannungsstoss durch #13 wird mit dem Komparator #40 auf Elektronik-level
gebracht. Zeitverzögert, durch das Monoflop #41, wird die Höhe des begrenzten Einschsltstromtoßes umgeschaltet,Fig.4
so das eine Anpassung an die Seond-Breakdown-kurve der Leistungstransistoren erfolgt Fig.3.dadurch erfolgt dann ein
schneller Anstieg der Ausgangsspannung. Fig.2
DC-converter inrush current is matched to transistor second breakdown. German Patent DE 31 31429 C2
The high voltages to supply microwave tubes for instance, Traveling wave tubes, is generated from space and weight
reasons in transistor DC converters. The switching transistors of the converter are often bidirectional transistors. Such a
converter is shown in Fig.1. the power transistors are # 10.11. When the supply DC voltage by the switch # 13 is
switched on, the converter has to fulfill two the two opposing condition's and *2
- *1 The inrush-current of the converter must not damage the Power-transistors
- *1 The inrush-current of the converter over the switching on time, must not override the second breakdown
specification of the Transistors.
- *1 The inrush--current must be as low as possible
- *2 The High voltages must come up in a certain short time to prevent defocussing of the tube.
- *2 The inrush-current must be as high as possible.
This opposing requirements can only be solved by means of a compromise. Fig.1 shows a converter which realizes a
compromise between requirement *1 and *2.
The components # 10,11,12,20,21,15,16,17, represent the actual converter. In order to satisfy the condition * 1, the
Inrush-current is hard limited, with the loop of the components # 31 , 32.33. # 32.33 are the amplifiers of the constant
current loop. In order to satisfy the condition * 2 the inrush current level is time-dependent changed. # 45,41,48. The
Inrush-current through # 13 is brought on electronic level with the comparator # 40th. By means of a Time delay, by the
one-shot # 41, the height of the limited inrush-current s is switched, (Fig.4) so that an adaptation to the Second
-Breakdown-curve of the power transistors occurs: Fig.3, what leads then to a rapid increase of the output voltage Ua. Fig.2
Fig.1 DC-Converter with Second Breakdown matched inrush-current /
Fig1 DC-Wandler mit an Second-Breakdown angepastem Einschaltstromstoß
Return:
|
|
|
|
Literature, readings: Power supply , switcher, electronic power conditioning, Netzteile
- R.Hayner
The venable converter, a new approach to power processing, In: IEEE Transaction, Vol. IECI-24, Nr.4 Nov.1977, p266.
- Silicon General, Zur Verbesserung des dynamischen Verhaltens von Schaltreglern.
- Erich
Pivit, Stabilitätsuntersuchungen an impulsbreitengeregelten Durchfluss und Sperrwandlern. Frequenz Jg.30 1977, Seite 96
- Wüstenhube, Schaltnetzteile 1979 expert Verlag Grafenau.
- Watkins Johnson : Design of Power converters for space TWTA’s.
Return:
|
|
|
|
British , American and German Wires at a Glance
Power-supply’s have Transformers and Transformers have Wires. The following tables, show
British , American and German Wires:
Return:
|
|